The boom in sustainable agriculture has driven a surge in demand for glufosinate ammonium, a non-selective herbicide favored by farmers for its effectiveness and eco-friendly profile. As the industry pivots towards more responsible farming practices, the role of glufosinate ammonium factories has become increasingly pivotal. This growth is not only a testament to the product's utility but also underscores the importance of high-quality manufacturing processes that prioritize safety, efficiency, and environmental stewardship.
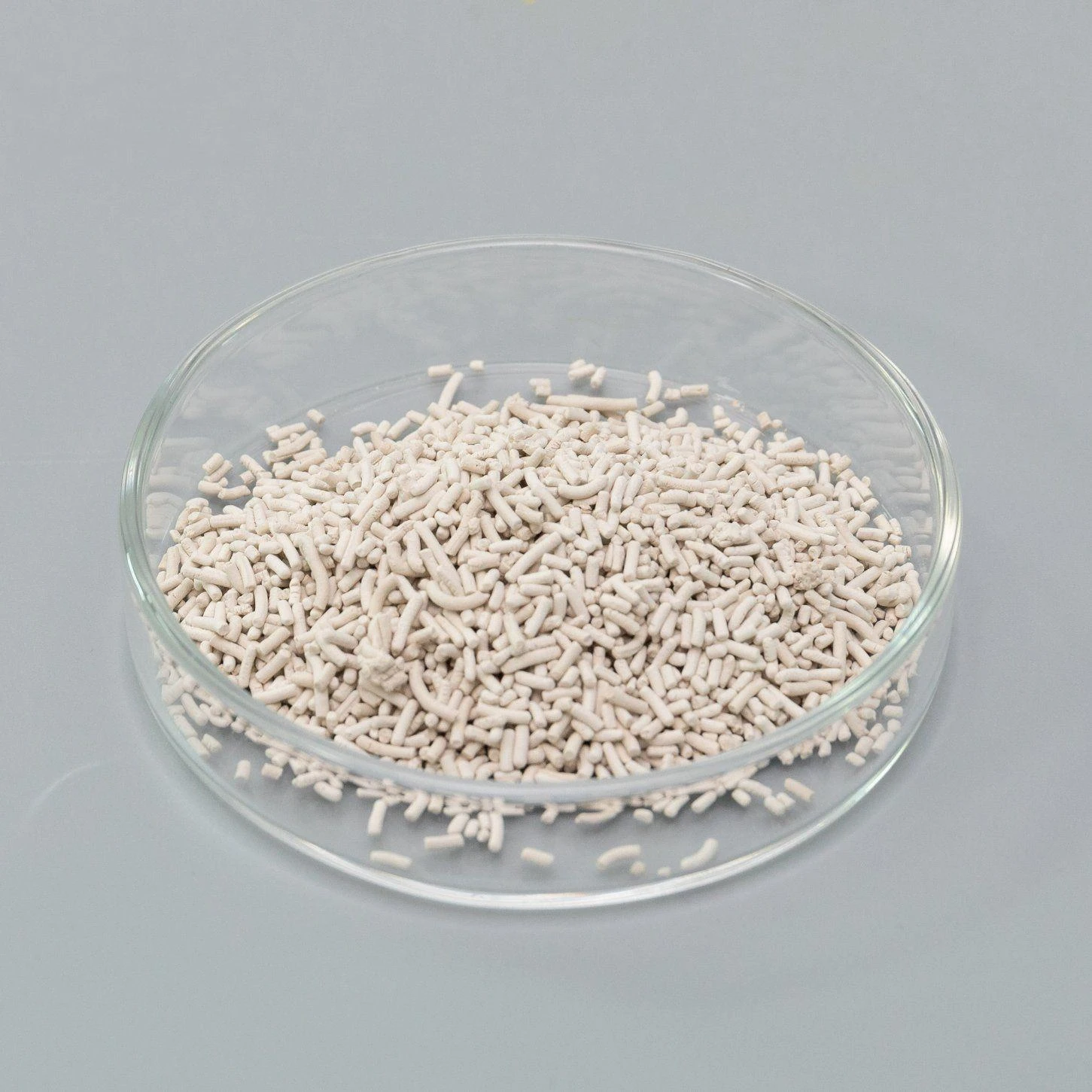
Experience within the industry indicates that the manufacturing of glufosinate ammonium is a complex process requiring a deep understanding of chemical reactions and a commitment to sustainable practices. Visiting one of these factories provides an enlightening perspective on how raw ingredients are transformed into a highly effective herbicide. Advanced technology and innovative production techniques are cornerstones of these facilities, ensuring that each batch of glufosinate ammonium meets stringent quality standards.
The expertise involved in manufacturing glufosinate ammonium is noteworthy. Chemists and engineers collaborate to optimize synthetic pathways, minimizing waste and maximizing yield. Through rigorous testing and continuous monitoring, these experts ensure that each product meets global regulatory standards. This process not only maintains the integrity of the product but also builds a foundation of trust with distributors and end-users.
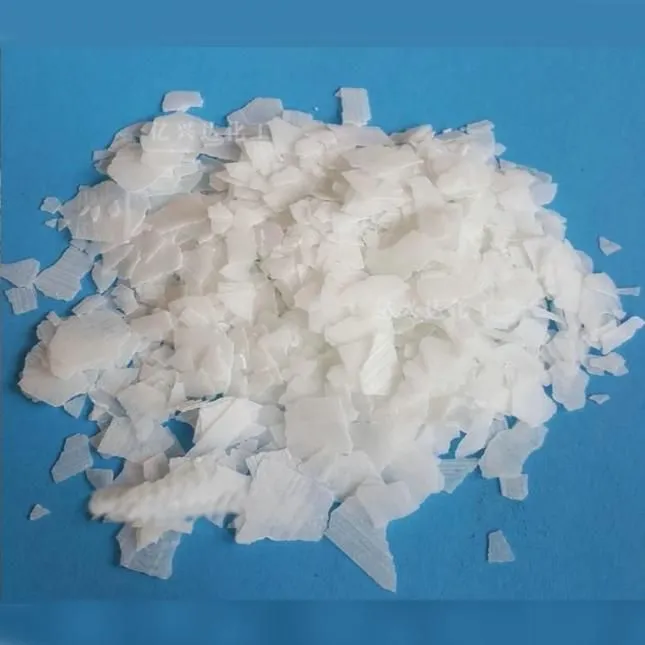
Authoritativeness in the realm of glufosinate ammonium factories is established through continuous investment in research and development. By staying at the forefront of agricultural science, these manufacturers contribute valuable insights into effective weed management strategies and sustainable farming practices. Partnerships with academic institutions further enrich the industry’s body of knowledge, promoting innovations that enhance crop yield and environmental compatibility.
glufosinate ammonium factory
Trustworthiness is a critical metric for any glufosinate ammonium factory. Transparent operations are essential, ensuring that stakeholders have full visibility of the manufacturing process and the product's lifecycle impact. Factories often undergo third-party audits to verify adherence to international standards, and their commitment to ethical practices is reflected in a responsible sourcing policy that prioritizes ethically produced raw materials.
From a product perspective, glufosinate ammonium is lauded for its versatility and efficiency in controlling a wide array of weeds without leaving harmful residues. This selectivity means it can be integrated into crop management systems without detrimental effects on the soil or surrounding ecosystems. As farmers face increasing challenges from invasive species and climate change, reliable solutions like glufosinate ammonium are vital for maintaining both productivity and ecological balance.
Sustainability is a core tenet of modern glufosinate ammonium factories. These facilities often implement robust waste management systems, recycling and reusing materials wherever possible. Emissions are closely monitored, and many factories have achieved significant reductions through the adoption of green technologies. Efficient energy use and the integration of renewable energy sources showcase the industry’s commitment to reducing its environmental footprint.
In summary, the landscape of glufosinate ammonium production is defined by a blend of technical expertise, strategic sustainability practices, and unwavering commitment to quality and transparency. As the global emphasis on sustainable agriculture intensifies, these factories position themselves as leaders in providing solutions that address the dual imperatives of feeding a growing population and preserving the planet's ecosystems. Through a relentless pursuit of excellence, glufosinate ammonium factories not only contribute to the agriculture sector's resilience but also champion a model of industrial responsibility that others can emulate.